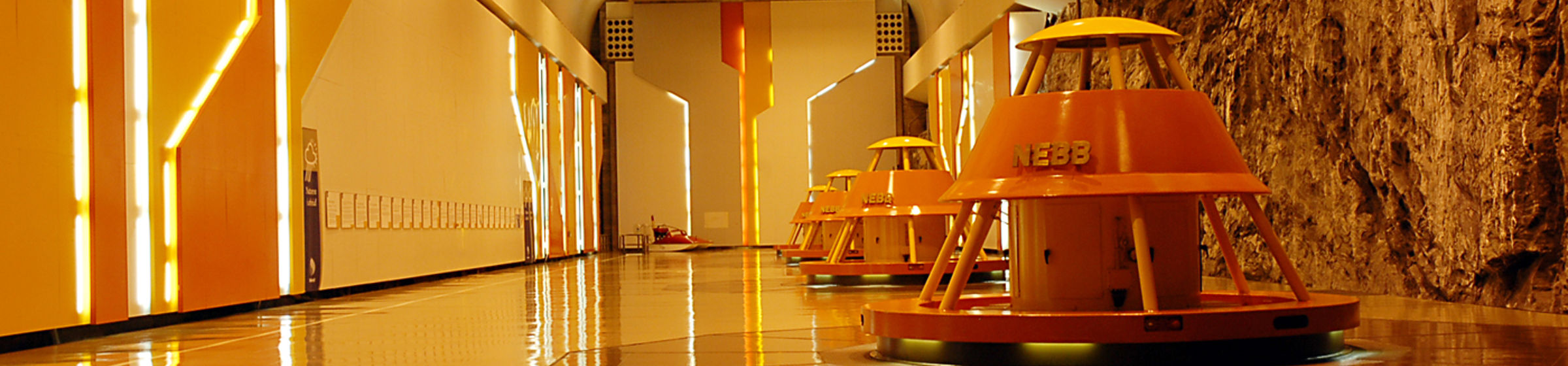
Maskinsalen i Kvilldal, Norges største vannkraftverk og en del av Ulla-Førre-utbyggingen.
Maskinlæring: Vil lære kraftverk å snakke
Vannkraftverkene drar på åra. Det betyr kostnadskrevende vedlikehold og store reinvesteringer. Hva om kraftverkene kunne fortelle hva de trengte når?
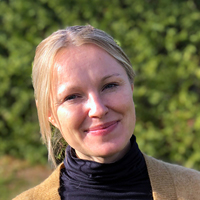
Camilla Feurst er spesialist i risikostyring i Statkrafts forretningsområde Norden.
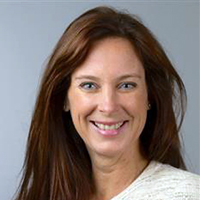
Christine Schei Liland har tittelen Business IT Developer og arbeider med datamodellering og prosjektledelse i Statkrafts forretningsområde for finans og IT.
Mange norske vannkraftverk ble bygget for mellom 50 og 100 år siden. De har nådd en alder der behovet for hyppigere vedlikehold og utskifting av komponenter øker. Dette er kostbare operasjoner. Hvert år bruker Statkraft opp mot to milliarder kroner på å vedlikeholde og utbedre den tekniske standarden til de verdifulle vannkraftverkene.
– Med tidligere og mer detaljert informasjon om vannkraftverkenes tekniske tilstand, kan vi operere med mindre marginer i vedlikeholdsplanleggingen og samtidig være trygge på at vi unngår feil, sier Camilla Feurst, spesialist i risikostyring i forretningsområdet Norden i Statkraft.
Spåkule
Det er her digitalisering kommer inn i bildet.
– Alle våre vannkraftverk er automatiserte, men risikovurderingene er i dag fortsatt basert på fysiske inspeksjoner og manuelle beregninger. Det betyr at potensialet for digitalisering er stort, sier hun.
I 2017 gjennomførte Statkraft et pilotprosjekt ved Kvilldal vannkraftverk for å undersøke hvorvidt avanserte dataanalyser, algoritmer og maskinlæring kunne gi ny innsikt om kraftverkenes tilstand og være nyttige verktøy for vedlikeholdsgruppene.
– Vi ønsket oss en spåkule og ville undersøke om datadrevne modeller kunne gi oss svarene vi trengte. Målet er å utnytte hele levetiden til deler og komponenter, samtidig som vi unngår havarier og ikke-planlagt nedetid på kraftverkene. Med mer presise risikovurderinger kan vi også minimere den planlagte nedetiden i tilknytning til vedlikehold og utbedringer, sier Feurst.
Nylig har innsiktene fra 2017 blitt brukt på nye måter ved Jostedal vannkraftverk.
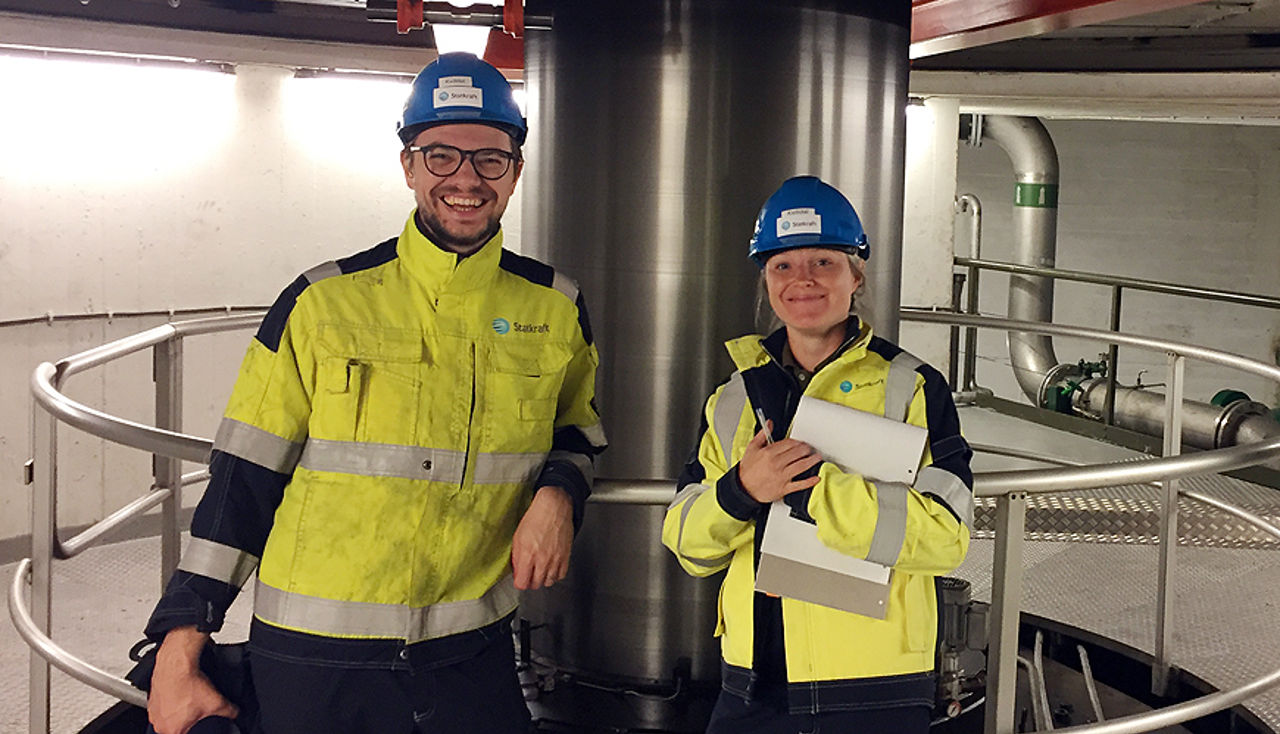
Fant endringer før svikt
Ved Jostedal har Feurst og en gruppe dataanalytikere kjørt en ny «helsemodell» innen maskinlæring som kan identifisere endringer i friske kraftverk. Her ble sensorer brukt til å oppdage avvik i det som ellers var et velfungerende kraftverk. Til sammenligning, ble det ved Kvilldal brukt maskinlæring etter at en uforutsett hendelse hadde funnet sted.
Under piloten oppdaget prosjektgruppen mindre endringer i noen sensorer. Det tok testen i en ny retning.
– Selv om kraftverket var i full drift den våren, hadde vi oppdaget små endringer i noen få sensorer. Vi var ikke sikre på om disse endringene var kritiske eller ei, så vi bestemte oss for å stoppe for inspeksjon, sier Feurst.
Da inspeksjonen skulle finne sted tre uker senere, sviktet et aksiallager 12 timer før inspeksjonsstart.
– Inspeksjonen kom akkurat for sent i dette tilfellet, men det var likevel en solid bekreftelse på at små endringer i data kan bety noe. Nå monterer vi ekstra sensorer og følger opp kraftverksgruppa på ukentlig basis for å sørge for at vi ikke opplever en lignende svikt, forklarer Feurst.
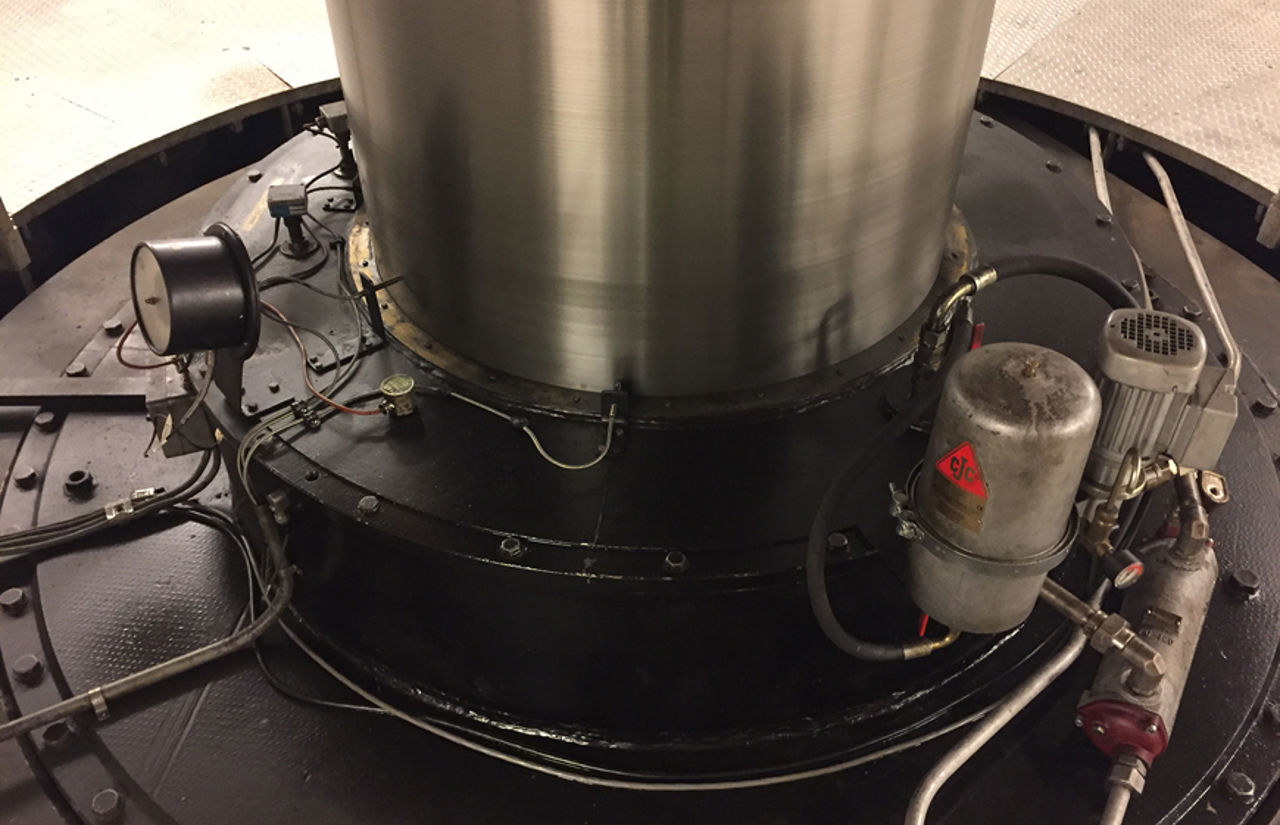
Uvurderlig ekspertise
Kunnskapen og intuisjonen man finner i menneskene som jobber på kraftverk, er umulig å erstatte. Feurst mener det er kombinasjonen av de ansattes ekspertise, tverrfaglige team og rike mengder data som har gjort deres prosjekt så lærerikt.
– Vedlikeholdslederen kan legge håndflaten på turbinen og med en gang føle om vibrasjonen ikke er som den skal. Men hva skjer når han slutter? For oss har det vært avgjørende å ha tett dialog med vedlikeholdsgruppen og suge til oss kunnskapen de sitter på. Mennesker med høy kompetanse har foretatt faglige vurderinger på kraftverkene i nærmere hundre år. Den opparbeidede erfaringen er svært verdifull. Også når vi skal lage gode datadrevne modeller, sier hun.
Når gammel og ny kunnskap møtes på denne måten, kan skepsis oppstå. Det var ingen overraskelse for Feurst.
– Sunn skepsis er nyttig og gjør prosjektet bedre, men frykt for at algoritmer og sensorer på sikt skal erstatte mennesker, kan gjøre oss mindre omstillingsdyktige. Vi kommer fortsatt til å trenge folk, men kanskje i litt andre roller enn i dag, sier hun og understreker:
– Vi må aldri glemme at modellene beskriver en virkelighet – og den vil alltid bestå av natur og mekanikk.
Når kraftverkene snakker
Da Camilla Feurst og dataanalytikerne ankom Kvilldal, møtte de en vedlikeholdsgruppe med flere tiårs erfaring fra anlegget.
– Vedlikeholdslederen kan legge håndflaten på turbinen og med en gang føle om vibrasjonen ikke er som den skal. Men hva skjer når han slutter? For oss har det vært avgjørende å ha tett dialog med vedlikeholdsgruppen og suge til oss kunnskapen de sitter på. Mennesker med høy kompetanse har foretatt faglige vurderinger på kraftverkene i nærmere hundre år. Den opparbeidede erfaringen er svært verdifull. Også når vi skal lage gode datadrevne modeller, sier hun.
At mange var litt skeptiske til prosjektet, var ingen overraskelse for Feurst.
– Sunn skepsis er nyttig og gjør prosjektet bedre, men frykt for at algoritmer og sensorer på sikt skal erstatte mennesker, kan gjøre oss mindre omstillingsdyktige. Vi kommer fortsatt til å trenge folk, men kanskje i litt andre roller enn i dag, sier hun og understreker:
– Vi må aldri glemme at modellene beskriver en virkelighet – og den vil alltid bestå av natur og mekanikk.
Når kraftverkene snakker
Som Jostedal-teamets erfaringer viser, er det ikke altfor lenge til kraftverk vil kunne si ifra selv når de «føler» at noe ikke er som det skal være. Sensorer, data og algoritmer kan påvise hvor problemet er, og fortelle når og hvordan det best kan løses.
– Kollegene våre på kraftverk jobber konstant med å feilsøke og dekode fysiske komponenter i anleggene våre. Nå kan vi bedre mulighetene deres til å oppdage selv de minste endringer ved hjelp av maskinlæring, slik at vi holder kraftverkene våre friske og i full drift, sier Feurst.
"Vi ønsket oss en spåkule og ville undersøke om datadrevne modeller kunne gi oss svarene vi trengte. Målet er å utnytte hele levetiden til deler og komponenter, samtidig som vi unngår havarier og ikke-planlagt nedetid på kraftverkene."